Gelatine Processing Plant
(Edible / Industrial / Pharma)
Gelatine is derived from Degreased Crushed Bones (DCB) through acid treatment followed by alkaline process. DCB are first treated with acid for removal of inorganic salts in bone. The bones after acid treatment are referred to as Ossein.
Ossein is then treated with alkali for partial hydrolysis. During the partial hydrolysis the collagen material is softened from the non-collagen. Non-Collagen gets removed with weak alkali solution. The temperature is controlled during maceration and liming to avoid any yield losses. Limed Ossein is then washed with water and then treated with dilute solution of weak acid. Ossein after weak acid treatment is taken for Gelatine extraction.
Gelatine is extracted in the form of weak liquor, which is then filtered and passed through ion exchange (deashing system) for reduction of the dissolved ash(dissolved minerals) in the gelatine solution. This de-ionised weak liquor of Gelatine is then concentrated under vacuum to avoid any destruction to the basic tri skeleton structure of gelatine. So our gelatine processing plant or gelatine extraction plant is very useful.
Concentrated liquor is then passed through sterilisation system followed by extrusion for making noodles to facilitate proper drying of Gelatine in the next stage.
Gelatine drying is very critical process since fast heating will melt the gelatine instead of drying and slow drying will result in gelatine moisture out of limits so Gelatine is dried very carefully with dehumidified air by gradual increase of temperature gradually to 60OC.
Dried Gelatine is then crushed to required mesh size as per the market demand. During Gelatine manufacturing DCP is produced as a byproduct. Which is a main constituent for the cattle and poultry feed.
General Block Diagramme Depicting Gelatin Manufacturing Process From Degreased Dry Bones
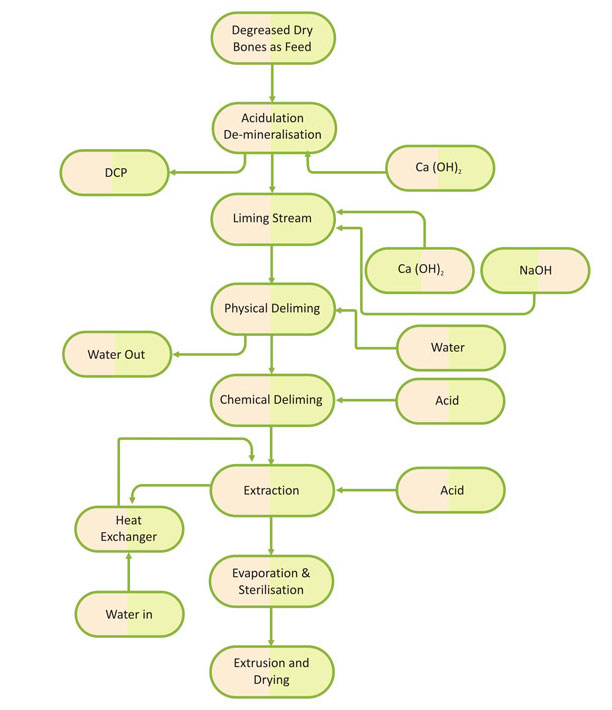
SSP'S UNIQUE DESIGN ENSURES
- High Product Quality.
- Compact design.
- Easy operation & automatic control.
- Minimum manpower required.
- Low operation cost.
- Easy Cleaning due to absence of fouling and hygienic construction.
- Continuous Production without product hold up.